Comparing 3D Scanning and Traditional Manufacturing Methods
Understanding 3D Scanning and Traditional Manufacturing Methods
In today's rapidly evolving industrial landscape, the choice between modern and traditional manufacturing methods is more critical than ever. Among the most notable advancements is 3D scanning, a technology that has transformed how products are designed and produced. This post explores the differences between 3D scanning and traditional manufacturing, providing insights into their advantages and potential applications.
What is 3D Scanning?
3D scanning is a process that captures the shape of an object using a laser or structured light to create a digital 3D model. This technology allows for highly accurate and detailed representations of physical objects, which can be used in various applications, from design to quality control. The ability to reverse-engineer existing products makes 3D scanning a powerful tool in innovation.
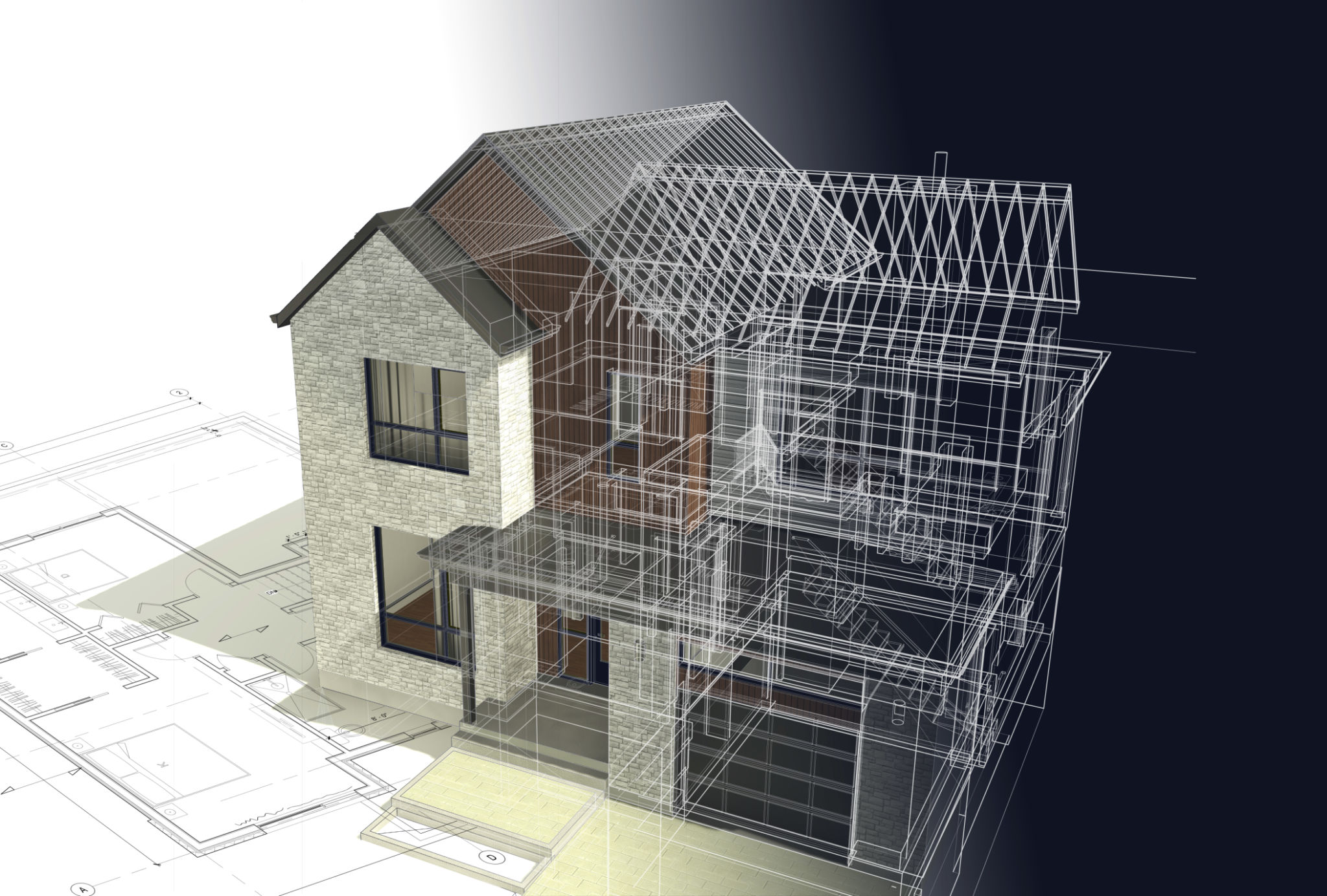
Traditional Manufacturing Methods
Traditional manufacturing methods, such as machining, casting, and forming, have been the backbone of production for centuries. These processes involve shaping materials into desired forms through mechanical means, often requiring extensive labor and time. While effective, traditional methods can sometimes be limited by material constraints and geometric complexities.
Despite these limitations, traditional manufacturing remains essential for mass production due to its cost-effectiveness and scalability. Industries like automotive and aerospace continue to rely heavily on these methods for producing large quantities of parts.
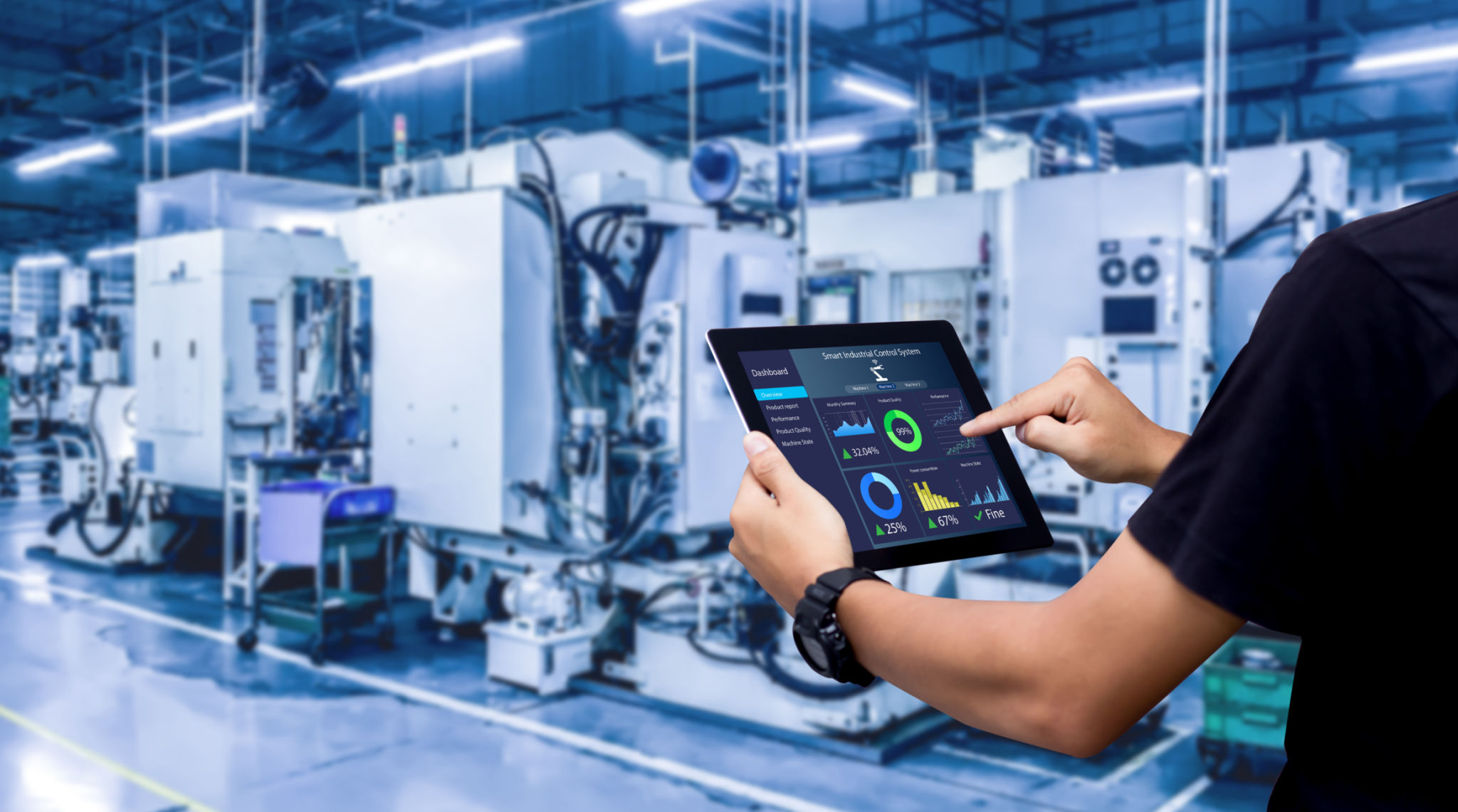
Advantages of 3D Scanning
The primary advantage of 3D scanning is its ability to create precise digital models quickly and efficiently. This capability allows for rapid prototyping, enabling designers to test and iterate on their concepts without the need for costly physical prototypes. Additionally, 3D scanning facilitates customization, allowing for personalized products and solutions tailored to specific needs.
Another significant benefit is its application in quality control. By comparing scanned models with original designs, manufacturers can detect deviations and ensure that products meet stringent quality standards. This process enhances reliability and reduces the likelihood of defects.

Comparing Costs and Efficiency
When it comes to cost and efficiency, both 3D scanning and traditional manufacturing have their own merits. Traditional methods are often more economical for large-scale production runs, where setup costs can be amortized over thousands of units. However, for smaller batches or prototypes, 3D scanning can be more cost-effective due to reduced material waste and shorter production times.
Efficiency also plays a crucial role in the decision-making process. 3D scanning offers a faster turnaround for complex parts, as it eliminates many of the manual steps involved in traditional manufacturing. This speed can lead to quicker time-to-market for new products.
Choosing the Right Method
The decision between 3D scanning and traditional manufacturing depends largely on the specific requirements of a project. For intricate designs requiring high precision or customization, 3D scanning is often the preferred choice. In contrast, traditional methods remain advantageous for projects demanding large volumes of standard parts.
Ultimately, many industries find that a hybrid approach—utilizing both technologies—yields the best results. By integrating the strengths of each method, manufacturers can optimize efficiency, quality, and cost-effectiveness.